A Practical Guide for Dental Compressed Air and Vacuum Systems in Day Procedure Centres
A dental compressed air and vacuum system (DAVS) is a central system providing compressed air and/or vacuum suction, and comprises sources of supply and a pipeline distribution system connecting to dental chair. The system aims to provide safe, convenient and cost effective compressed air and/or vacuum suction for dental staff at the point of use, and ensure patient and staff safety. This system is not applicable to portable compressed air equipment, portable suction source equipment, and the localised equipment forming part of a proprietary dental chair with compressor or vacuum pump unit, and interconnection tubing matched to the needs of the air instruments therein.
Many dental day procedure centres require compressed air to power dental instruments and a vacuum system to remove detritus from the operation site. Where dental compressed air and vacuum systems are installed in day procedure centres, licensees may refer to Annex III of the Code of Practice for Day Procedure Centres (i.e. Guidelines for Dental Compressed Air and Vacuum Systems) for general guidance on the design and installation of such systems. To facilitate prospective applicants of day procedure centre licences and licensees of existing facilities familiarizing with these systems, this office has compiled a practical guide and associated pamphlet in order to outline the key points to note regarding design, installation, operation and maintenance of these systems, including examples of DOs and DON'Ts, for facilitating the safe and effective delivery of medical services in healthcare facilities.
The following guide is for general reference and information purposes only, and should be read in conjunction with the latest version of the Code of Practice for Day Procedure Centres, other applicable ordinances, regulations and codes.
- The manufacture, storage, supply and use of a DAVS in the facility comply with all relevant statutory requirements, including but not limited to those stipulated under the following Ordinances and their subsidiary legislations and codes of practice:
(a) Dangerous Goods Ordinance (Cap. 295);
(b) Fire Services Ordinance (Cap. 95);
(c) Electricity Ordinance (Cap. 406); and
(d) Boilers and Pressure Vessels Ordinance (Cap. 56). - The design and installation of the DAVS meet internationally acceptable healthcare standards such as Health Technical Memorandum (HTM) 2022 – Supplement 1 (2003 edition) – Dental compressed air and vacuum systems, or equivalent.
1. General requirements |
✓ |
Engage competent service providers (including a registered professional engineer) with relevant qualification and experience since early design stage to carry out design, installation and certification of DAVS. (Template of Certificate of compliance with healthcare engineering requirements) |
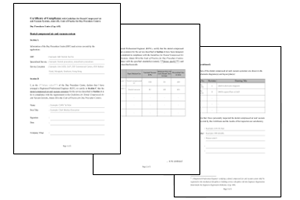 |
✓ |
Provide DAVS plants and equipment with standby unit and connect to back-up power supply to ensure continuity and security of the system operation during normal and contingent situations. Where it is not feasible to provide standby unit or back-up power supply for the plants and equipment, an emergency response policy should be established to ensure patient safety in that event. |
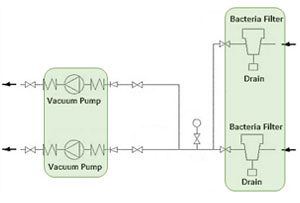
Example: System with standby unit (1 duty 1 standby)
|
✓ |
Conduct testing and commissioning for new installations and additions or alterations to existing installations of DAVS. |
Examples of tests are: (a) functional tests; (b) tests for cross connection; (c) tests for leakage; (d) tests for flow; (e) tests for pressure; (f) tests for safety valves; (g) tests of warning system; and (h) tests for air quality. |
✓ |
Ensure adequate capacities of the DAVS plants to meet the system demand of air flow and pressure for safe operation of dental instruments. |
Example: Equipment specification of air compressor: (specify information such as number of dental chairs supported, gas flow and pressure)
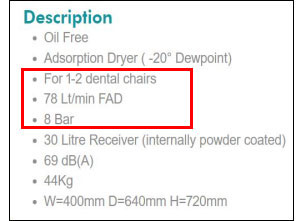 |
2. Dental Compressed Air Systems |
✓ |
Fit a bacteria filter at the downstream of the dental compressed air system. |
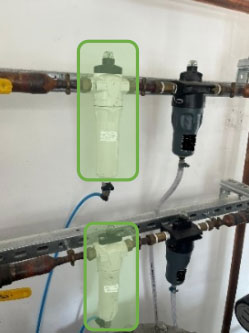
Example 1: Bacteria Filter in Large-scale System
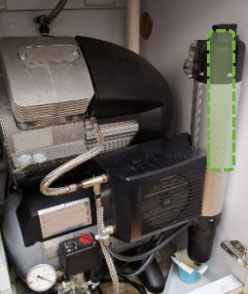
Example 2: Bacteria Filter in Small-scale System |
✓ |
Provide gas-specific test point to facilitate the air quality test. |
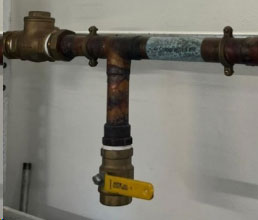 |
3. Dental Vacuum Systems |
✓ |
Locate air outlet(s) of dental vacuum system outside the building on the condition that the air outlets are away from air intakes and opening windows. Where it is not feasible to locate air outlet outside the building, the exhaust line is provided with a filter complying with the following requirements or manufacturer's recommendation:- providing particle removal to 0.01 μm with a filtration efficiency of not less than 99.9999% under dispersed oil particulate (DOP) test, at class U16 in accordance with EN 1822, or equivalent; and
- removing unpleasant odours arising from the system.
|
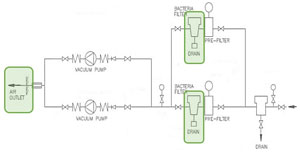
Example of good practice: Air outlet is located outside the building and bacteria filters were provided
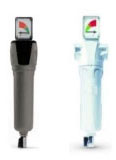
Example of Filter Unit |
✓ |
Install the dental vacuum system with separator unit. |
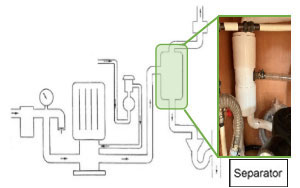
Example: Vacuum system with separator unit to separate air and water |
✘ |
Locate the equipment at space with poor ventilation and lack of maintenance space. |
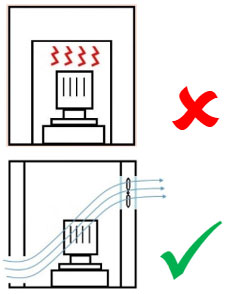 |
✘ |
Abandon test records, operation and maintenance manual, and as-fitted drawings. |
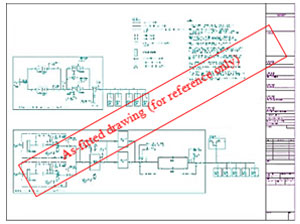 |
✘ |
Omit the dryer, separator unit and bacteria filter in the design of dental compressed air system. |
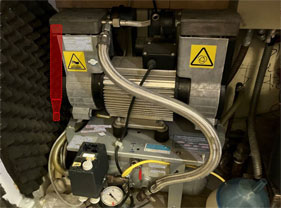
Dryer, separator unit and bacteria filter generally can be provided as an optional item |
✘ |
Discharge exhaust air from dental vacuum system directly to the drainage system without any suitable separator unit. |
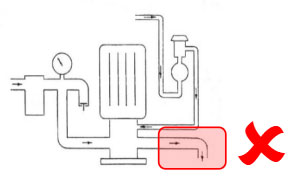 |
✘ |
Locate air outlet of dental vacuum system directly inside the building without any suitable filter unit. |
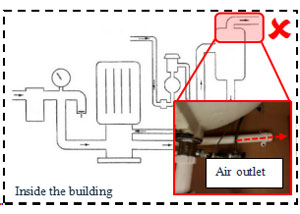 |
Operation and Maintenance
The DAVS is properly operated and maintained, complying with all applicable statutory requirements, and taking into consideration of the guidance given in internationally acceptable healthcare standards such as HTM 2022 – Supplement 1 (2003 edition) or equivalent, the manufacturers' recommendations and good trade practices.
- Ensure operation and maintenance schedule for DAVS in place.
- Arrange the schedule of general operation practices with reference to the recommendation of internationally acceptable healthcare standard. Examples are:
☑ |
Clean out large particle filters |
Daily /
According to manufacturer's recommendation |
☑ |
Switch off the compressor (for small compressor unit) |
Daily /
According to manufacturer's recommendation |
☑ |
Clear the flask / collector tray of drain valve for air receiver and dryer unit (if applicable) |
Daily / According to manufacturer's recommendation |
☑ |
Check oil levels of lubricated plant (if applicable) |
Weekly /
According to manufacturer's recommendation |
☑ |
Empty the receivers of air compressors (for receivers that are not fitted with automatic drains) |
Weekly / According to manufacturer's recommendation |
- Arrange service agent to conduct routine maintenance with reference to the recommendation of internationally acceptable healthcare standard. Examples are:
☑ |
Change filter elements |
Yearly / According to manufacturer's recommendation |
☑ |
Check the function and performance of the compressor and vacuum plant |
Yearly / According to manufacturer's recommendation |
☑ |
Carry out air quality test |
Yearly /
According to manufacturer's recommendation |
☑ |
Change the separator unit |
According to manufacturer's recommendation |
☑ |
Inspect the air receiver, its fittings and attachments by an appointed examiner |
Refer to the requirements stipulated in Boilers and Pressure Vessels Ordinance (Cap. 56) |
- Ensure maintenance record of DAVS being properly kept. The maintenance log should record the following information:
☑ |
Date and Time |
☑ |
Nature of maintenance work (e.g. routine or corrective) |
☑ |
Identification of equipment (e.g. equipment number, serial number, model etc.) |
☑ |
Scope of works |
☑ |
Condition of equipment |
☑ |
Replaced parts (if applicable) |
☑ |
Information of the contractor/worker |
- Emergency call-out service arrangement is in place with a specialist contractor.
- Perform air quality test for dental compressed air system regularly. Compressed air quality parameters as recommended in the internationally acceptable healthcare standard include, but not limited to, oil, water, particulate, oxygen, nitrogen, carbon dioxide, carbon monoxide, sulphur dioxide, nitric oxide and nitrogen dioxide.
|
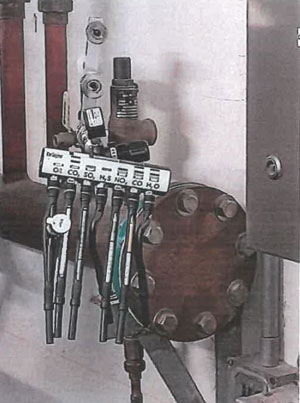
Air quality test |
Examples of service providers for air quality test:- Organization accredited under The Hong Kong Laboratory Accreditation Scheme (HOKLAS) published by Hong Kong Accreditation Service;
- Specialist contractors limited to supply and installation of medical gas system under the List of Approved Suppliers of Materials and Specialist Contractors for Public Works (Steam and Compressed Air Installation) published by Development Bureau.
Disclaimer:
The above lists are by no means exhaustive and are for reference only. The lists are compiled, maintained and provided by various government departments, professional institutions/associations or trade unions. The Office for Regulation of Private Healthcare Facilities (ORPHF) plays no part in compilation of the lists and shall not be responsible for any inaccuracies in the lists nor any error/incomplete information arising from the hyperlink nor any loss or damage whatsoever arising out of or in connection with any information or the performance of the persons/companies in the lists. The persons/companies in the lists should not be regarded as endorsed or recommended by the ORPHF. The responsible persons of the healthcare facilities are responsible for making their own verification of all information in the lists. Related organisation should be contacted should there be any queries on any matter regarding the lists.
The electronic pamphlet with practical information is also available for download (Traditional Chinese version available only).
Pamphlet for Dental Compressed Air and Vacuum Systems in Day Procedure Centres